
Nieuw proces maakt waterstof uit huisvuil
Veel huishoudelijk afval wordt verbrand. Dat levert warmte en elektriciteit op, maar dit zijn laagwaardige toepassingen. Ingenieurs bij RWE hebben iets beters bedacht: een proces dat het huisvuil afbreekt tot moleculaire bouwstenen.
Glas gaat naar de glasbak, papier in een container, plastic flesjes en blikjes gaan sinds kort naar de supermarkt voor statiegeld. Maar voor de grote berg vuilnis die overblijft nadat alle nuttige materialen eruit zijn gehaald, zijn er momenteel maar twee opties: storten of verbranden.
Storten wil eigenlijk niemand meer en verbranden levert weliswaar nog warmte en elektriciteit op, maar waardevolle en schaarse moleculen verdwijnen in de lucht.
Ingenieurs bij energiebedrijf RWE bedachten een proces om dat niet-recyclebare huishoudelijk afval om te zetten in syngas, een mengsel van waterstof (H2) en koolmonoxide (CO), en zo waarde eruit te halen. Syngas is weer om te zetten in allerlei andere stoffen, zoals methanol en ethanol.
Het gaat om circa 700.000 ton afval per jaar, 10 procent van wat in ons land wordt verbrand. Het proces noemden ze Furec: fuse, reuse, recycle.
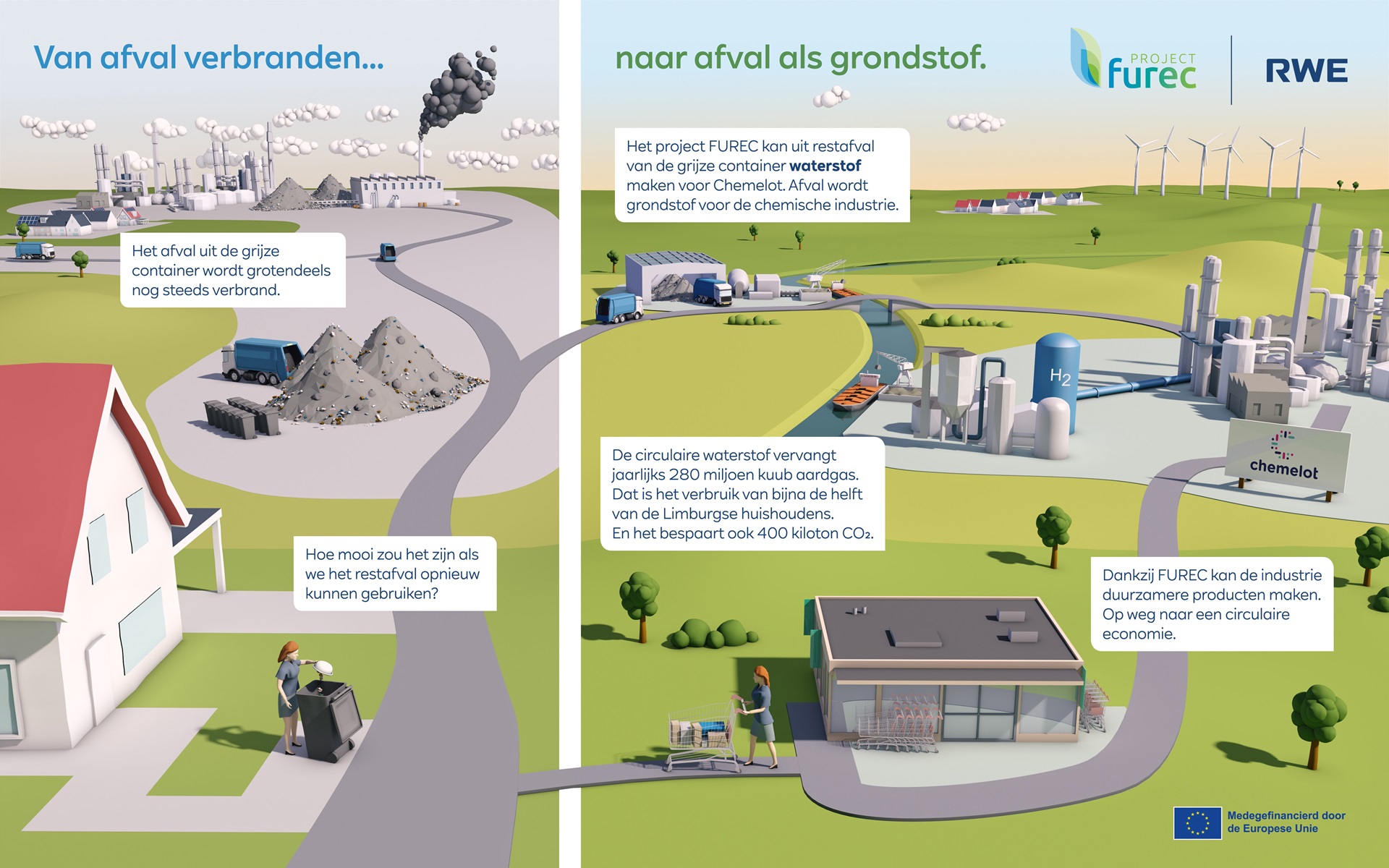
Lego
‘Simpel gezegd gaan de C- en H-atomen bij verbranding verloren doordat ze de lucht in gaan’, zegt uitvinder van het proces, Jan Eurlings. ‘Met ons proces behouden we die C’tjes en H’tjes en komen ze weer beschikbaar als grondstoffen voor de chemische industrie. Voor mijn kinderen vergelijk ik het proces met bouwen met Lego. Als je een bouwwerk beu bent, breek je het weer af tot losse legosteentjes. Dat is wat wij ook doen.’
Drogen, scheiden en verdichten
Het Furec-proces bestaat uit twee stappen. Eerst wordt het afval gedroogd, gescheiden en verdicht, en daarna afgebroken tot moleculaire bouwstenen. De eerste stap, waarvoor RWE een proces wil inrichten op industrieterrein Zevenellen in het Limburgse Haelen, begint met een bonte mengelmoes van afvalmaterialen. Deze stroom gaat eerst een shredder in, die het afval vermaalt tot stukjes van ongeveer een vinger lang. Dan wordt deze afvalberg elektrisch gedroogd.
‘We wilden geen fossiele brandstof meer gebruiken voor dit droogproces’, vertelt project engineering manager Eurlings. ‘Daarom gingen we op zoek naar een elektrische drooginstallatie. Toen we er geen konden vinden die aan onze specificaties voldeed, hebben we er zelf maar een ontworpen. Inmiddels
hebben we daarop patent gekregen.’
Sterk magneetveld
Na het drogen haalt een grote magneet de magnetische metalen uit het rulle materiaal en een wervelstroomscheider verwijdert de niet-magnetische metalen, legt engineering manager Carlo de Best uit. Onder invloed van een sterk magneetveld (eddy current-techniek) worden deze deeltjes tijdelijk magnetisch. Ze springen dan op de lopende band kort op, zodat ze zijn af te vangen.
‘Minerale fracties, zoals steen, scherven van serviezen of bloempotten, worden er met een windzifter uit gehaald’, zegt De Best. Daarbij scheidt een luchtstroom de zware van de lichte fractie. Wat overblijft is de brandbare fractie van plastics en biogeen materiaal, zoals spaanplaat uit meubels en katoen of ander textiel. Dat gaat opnieuw een shredder in die het tot stukjes van een paar centimeter maalt. Een laatste machine perst de afval snippers tot pellets van vijf centimeter lang en zestien millimeter doorsnede. ‘Hiervan is het vochtgehalte laag, lager dan 10 procent.’
In deze vorm zijn de pellets – zie de foto hieronder – rendabel te transporteren naar een andere locatie voor het tweede deel van het proces: het kraken van de chemische verbindingen. Veel stappen rond het innemen van het afval en het persen van de pellets zijn innovatief, zegt Eurlings. ‘Daar hebben we acht patenten op aangevraagd, waarvan er al vier zijn goedgekeurd.’
Huisvuil vergassen
De omzetting van de pellets tot waterstof gaat met een proces dat veel lijkt op steenkoolvergassing. ‘Dit is een klassiek proces uit de chemie, met als enige verschil dat bij ons het startmateriaal geen steenkool is, maar huishoudelijk afval. Beide zijn een verzameling koolstof- en waterstofatomen die onderling zijn verbonden. Maar waar steenkool eenvoudig is te verpulveren, daar is voor onze pellets nog een tussenstap nodig.’
Eurlings: ‘Direct vermalen lukte niet, dan smeren we ze helemaal uit. De materialen zijn te taai.’ Daarom roosteren de pellets eerst nog een halfuur in een heteluchtoven, waar ze pikzwart en bros uitkomen. Na malen blijft er fijn poeder over van korreltjes van minder dan een halve millimeter groot, geschikt voor de steenkoolvergassingstechniek. Het poeder wordt een reactor ingeblazen met een ondermaat aan zuurstof, bij een enorm hoge temperatuur van gemiddeld 1500 graden Celsius, lokaal wordt het wel 3000 graden.
‘Hierdoor gaan alle verbindingen tussen de C’tjes en de H’tjes kapot. We beginnen met een kakofonie aan koolwaterstoffen, maar wat overblijft is enkel syngas: een mengsel van waterstof en koolmonoxide, met restjes methaan.’ Dit moleculaire sloopwerk heeft als voordeel dat zelfs medicijnen en problematische
verbindingen, zoals PFAS, worden afgebroken. Het gevormde syngas wordt met water afgekoeld tot 200 graden Celsius. Het gas reageert met de hete stoom en een katalysator tot waterstof en CO2. De restjes zwavel die er in de vorm van waterstofsulfide (H2S) nog in zitten haalt de volgende stap (gasreiniging) eruit. Dit levert vloeibare zwavel, ook een grondstof voor bedrijven op het terrein.
Op naar Chemelot
Bij Chemelot, het enorme terrein met chemische bedrijven in Sittard-Geleen, komt de eerste installatie te staan die de aangevoerde pellets verwerkt en er syngas of water stof en CO2 van maakt voor bedrijven op de Chemelot-site. RWE is van plan de pellets over de Maas via de haven van Stein naar Chemelot te verschepen. Door de afvalpellets per schip te vervoeren, hoeven er elke werkdag circa 55 trucks minder heen en weer over de snelweg A2 te rijden. Minder overlast voor de omgeving dus. ‘En hoe mooi zou het zijn als die schepen straks varen op waterstof dat wij zelf hebben geproduceerd?’, zegt projectdirecteur Denis Aarssen.

Van syngas zijn met bekende processen verschillende nuttige stoffen te maken, zoals ammoniak, methanol en ethanol, zegt Eurlings. Op het terrein zitten bijvoorbeeld Sabic, dat ethyleen en propyleen produceert, en OCI Nitrogen, dat ammoniak produceert voor kunstmest. ‘Bij Chemelot is zoveel vraag naar waterstof, dat wij wel tien van dit soort units zouden kunnen neerzetten’, zegt Aarssen.
Hij wijst op het voordeel dat het kooldioxide al ‘zuiver in de hand is’, zoals technologen dat noemen. ‘We hoeven geen aanvullende investeringen te doen om CO2 te vangen (CO2-capture) of het nog verder te concentreren. Je zou CO2 onder de grond kunnen opslaan, en daarmee zelfs negatieve emissies bereiken. Maar eerlijk gezegd verwachten wij dat de vraag naar deze bouwsteen zal toenemen.’ Het kooldioxide is bijvoorbeeld interessant voor drankproducenten die er hun bier of frisdrank prik mee geven, of voor de productie van ureum, de grondstof voor de kunststof melamine en voor de vloeistof AdBlue, die
dieselmotoren schoner laat draaien.
Slakken en ertsen
In de pellets zitten nog verontreinigingen zoals zand en zware metalen, die in de vergasser smelten en langs de wand van de reactor een waterbad in lopen. Daar stollen deze resten tot slak, een soort donker glas, ‘een perfecte manier om zware metalen in te kapselen, zodat ze er niet kunnen uitlekken’, zegt Eurlings. Dit kan als betongrind in de bouw worden gebruikt.
De vluchtige zware metalen, zoals koper, lood en zink, vormen in de vergasser verbindingen met zwavel in afwezigheid van zuurstof. Bij afkoeling van het syngas condenseren deze metaalsulfiden en worden ze afgevangen in het waswater en neergeslagen als slib. ‘Die halen we in geconcentreerde vorm eruit. Dat mengsel is goed te vergelijken met zinkerts, zoals dat normaal met mijnbouw wordt gewonnen’, aldus Eurlings. Deze reststroom is interessant voor de metaalindustrie.
Overal inzetbaar
Terwijl RWE de pellets nu slechts dertig kilometer verder op inzet voor de volgende stap, zijn de gedroogde en verdichte korrels ook prima geschikt om over grotere afstanden te worden vervoerd. Aarssen: ‘Zo kan een fabriek in Portugal de pellets produceren uit het lokale huisvuil en die naar Rotterdam varen, waar een Furec-centrale er waterstof en kooldioxide van maakt. Met als afzetmarkten de Rijnmond of het Ruhrgebied via pijpleidingen die nu worden aangelegd door Gasunie en Delta Rhine Corridor.’
RWE denkt dat het Furec-proces overal in de wereld zijn nut kan bewijzen. ‘Het is een platformtechnologie die goed te herhalen is op een locatie waar vraag is naar waterstof en koolstof ’, zegt Aarssen. De EU kende het ontwikkeltraject eerder dit jaar dan ook een subsidie toe van 108 miljoen euro. Momenteel is RWE bezig om van de ontwikkelfase te komen tot een investeringsbesluit in de tweede helft van 2024.
‘Concreet betekent dit dat wij vergunningen aanvragen en verschillende aansluitingen op het stroomnet en op pijpleidingen voorbereiden’, aldus Aarssen. ‘Daarnaast werken we ook aan contracten met leveranciers en afnemers.’
In 2027 moet het eerste syngas worden geproduceerd. ‘Nog tijdens de bouw van de eerste Furec-installatie op Chemelot gaan we andere locaties bekijken voor toekomstige installaties.’
Foto's: Depositphotos; illustraties RWE