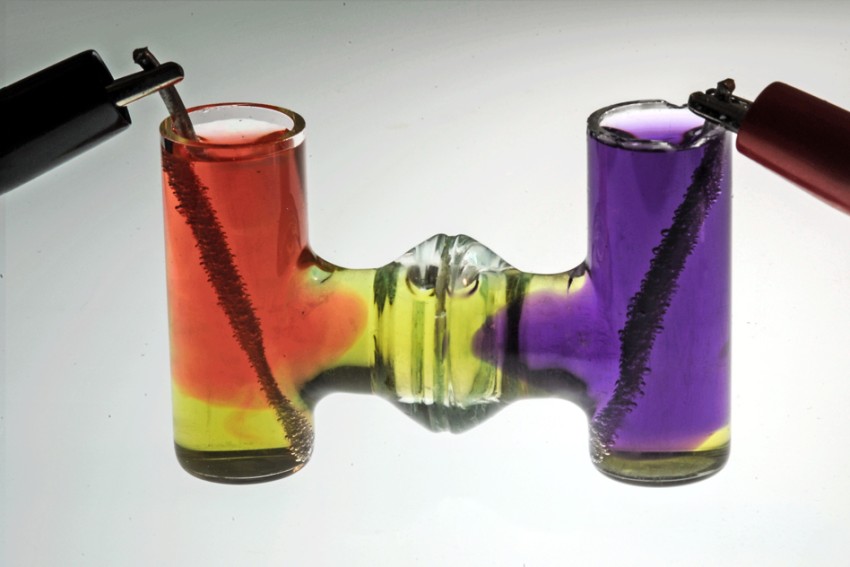
Doorbraak in ontwikkeling 'groen' cement
De cementproductie is een van de voornaamste bronnen van CO2-uitstoot. Onderzoekers in de Verenigde Staten hebben nu een doorbraak bereikt bij de productie van 'groen' cement, met een veel lagere ecologische voetafdruk.
Bij elke kilo cement die wordt gemaakt komt een kilo CO2 vrij. De cementindustrie neemt daarmee liefst 8 procent van alle CO2-uitstoot voor haar rekening. Onderzoekers proberen al jaren manieren te vinden om die uitstoot te verminderen. Maar de alternatieven zijn vaak te duur.
Een team van MIT zocht zijn heil in het gebruik van een elektrochemisch proces, en met succes. Ze publiceerden hun bevindingen maandag in het wetenschappelijke tijdschrift PNAS.
Gebluste kalk
De nieuwe productiewijze zoals de MIT-onderzoekers die beschrijven, draait rond een elektrolyseapparaat. De werking ervan is bekend: een batterij is verbonden aan twee elektroden in een glas water, waarbij de watermoleculen door de stroom uit de batterij worden gesplitst.
De ene elektrode produceert zuurstofbellen, de ander waterstofbellen. Belangrijk in dit verband: de zuurstofmakende elektrode geeft een zuur af, terwijl de ander een basisch milieu creëert.
Zuivere prik
Bij de MIT-methode wordt vermalen kalksteen - het voornaamste bestanddeel van cement - opgelost in het zuur. Daarbij komt uiterst zuivere koolstofdioxide vrij. Bij de andere elektrode ontstaat erdoor calciumhydroxide, oftewel gebluste kalk.
Van die calciumhydroxide kan vervolgens cement worden gemaakt, terwijl de koolstofdioxide, in de vorm van een pure, geconcentreerde stroom, eenvoudig kan worden geïsoleerd en opgevangen. Volgens de onderzoekers kan er onder meer vloeibare brandstof van worden gemaakt en kan het zelfs als 'prik' in frisdranken worden verwerkt: zo zuiver is het.
Normaal gesproken wordt cement gemaakt door kalksteen te vermalen en het vervolgens op hoge temperatuur te koken met zand en klei. Voor het verhitten worden kolen gebruikt. De grote hoeveelheid koolstofdioxode die daarbij vrijkomt, is vervuild met stikstofoxiden, koolstofmonoxide en andere stoffen die het ongeschikt maken voor verder gebruik.

Geen uitstoot
Bij het volledige productieproces hoeft geen CO2 meer vrij te komen, benadrukt onderzoeksleider Yet-Ming Chiang, hoogleraar materiaalwetenschappen, in een persbericht van MIT. De waterstof en de zuurstof die wel vrijkomen, kunnen worden gecombineerd in een brandstofcel. Dat moet genoeg energie opleveren om het hele productieproces op gang te houden, zegt medeonderzoeker Leah Ellis. De enige reststof die dan overblijft, is waterdamp.
Maar de onderzoekers zijn er nog niet. Tot nu toe hebben ze de vereiste elektrochemische stappen enkel getest in het lab, waarbij ze erin slaagden om uit het calciumcarbonaat calciumoxide te maken, de bouwsteen van cement. Nu gaan ze het op grotere schaal testen.
Duurzame bouw
De vraag naar duurzame bouwmaterialen is groot. Tot het jaar 2060 zal het aantal gebouwen op de wereld naar verwachting verdubbelen. 'Elke dertig dagen wordt er een stad gebouwd ter grootte van New York', stelt Chiang.
Cement is extreem populair omdat het weinig kost: ongeveer tien cent per kilo. Volgens de onderzoekers kan cement dat volgens de nieuwe, duurzame methode wordt gemaakt voor een concurrerende prijs worden aangeboden. Het cement zou bovendien van exact dezelfde samenstelling en kwaliteit zijn als het gebruikelijke portlandcement.
Beeld: Felice Frankel