
Organically formed concrete floor over fifty percent lighter
The organically formed concrete floor for an experimental house of Swiss technical university ETH weighs less than half as much as a conventional version. What's more, it looks great too. This floor has been made possible using design software and 3D printing.
It was made by engineers from ETH-Zürich and is part of the DFAB House, a demonstration project showcasing digital techniques in architecture. The floor rests on an unusually shaped basement wall, and supports a two-storey timber building.
The thinnest section is just 2 cm
The floor is borne in the middle by the unusually shaped basement wall and at the edges by straight wooden walls. The design is fully geared to that, with the basement wall being scanned down to the millimetre.
Software created the design in such a way that each point of the floor provides sufficient strength with as little material as possible. The floor is no thicker than 2 cm at its thinnest point. In addition, the underside of the floor has to contribute to acoustic quality.
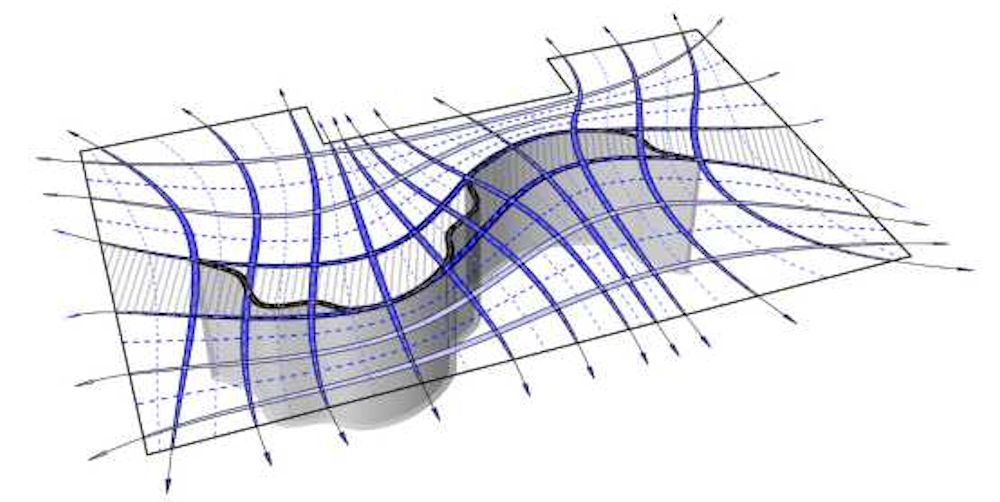
The floor was thereby given a structure that ensures the ribs provide load-bearing capacity, while the finer structures are there for acoustics and aesthetics.
Sandstone mould
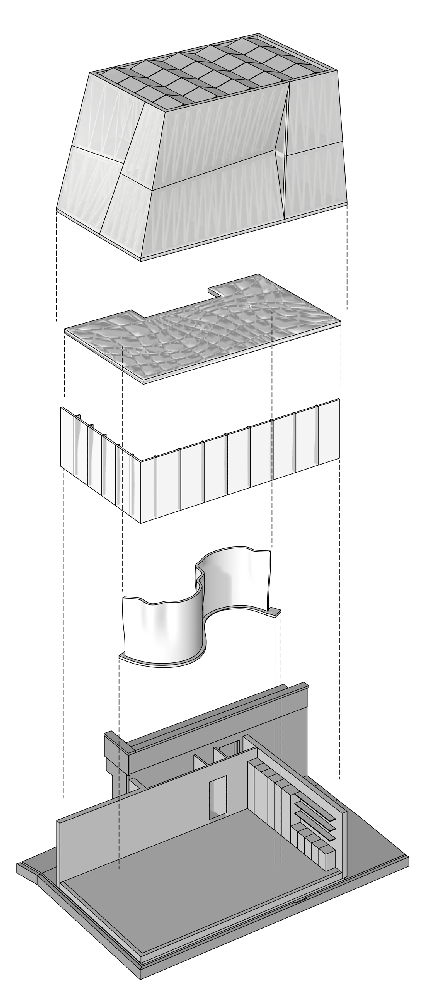
3D printing is very well suited to creating such an unusual shape. But contrary to directly printing concrete (read 'Concrete bicycle bridge from a printer'), the 3D printer is used here to create a sandstone mould for the floor. This is because the Swiss engineers wanted to use reinforced concrete for their floor, and it's not yet possible to use that material for 3D printing.
The mould was printed in sections of sandstone that were then linked together seamlessly. This gave the mould the shape of the floor section to be cast. The upper section of the casing was made of wood using a laser cutter to create hollows in the floor, to save weight and ensure space for fitting pipes and anchor cables.
Prestressed
Subsequently, the fibre-reinforced concrete was first sprayed onto the sandstone mould, and then filled up to the wooden casing.
At the construction site, the cast floor sections were then placed over the basement and prestressed using anchor cables. The production technique used ensures precise dimensioning, which makes it relatively easy to fit the floor sections together and prestress them. Thanks to the prestressing, the floor has a much greater load-bearing capacity.
The intention is that the DFAB House in Dübendorf, Switzerland, will be complete within the year.
If you found this article interesting, subscribe for free to our weekly newsletter!
See below how a robot makes the curved basement wall.