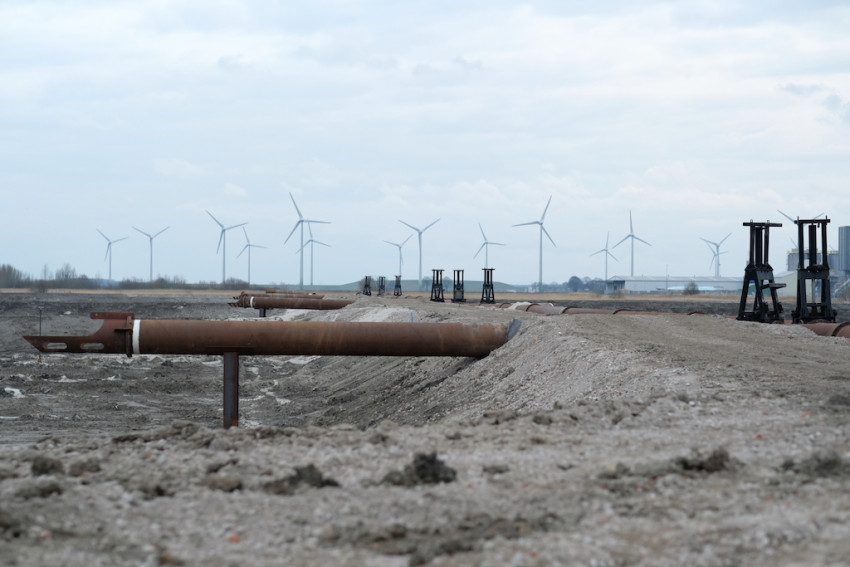
Trial to produce clay from sea sludge
As of today, engineers in Groningen are working at converting bay mud into clay. A dredging ship will collect sludge from the Eems-Dollard estuary and barge it to depots, where it will spend three years being compacted into clay strong enough to reinforce dikes.
The trial is a collaboration between the EcoShape knowledge consortium, the province of Groningen, and Rijkswaterstaat. ‘Clay is now often brought in from other parts of the country, even though there's more than enough sludge here in the estuary', explains Jannes Boer, project manager at EcoShape, on the telephone. ‘If we can produce it locally, that will be a solution for this excess sludge, so we'll be killing two birds with one stone.’
The sludge has a detrimental effect on water quality. It affects the ecosystem, resulting in less and less aquatic life in the Eems Dollard estuary and declining biodiversity. In the meantime, the dikes require reinforcement in order to continue providing protection from the water in the Wadden Sea. And that reinforcement process needs large volumes of clay.
UNIQUE PITS
The sludge will be dumped in a depot featuring 15 pits, each one around 1 hectare in size and 1.5 m deep. Each pit uses a unique technique in order to transform the sludge into clay as quickly as possible. 'The first pit we're filling this morning does not use any particular drying technique. However, in other sections we've added drainage systems, dug little ditches to drain the water quickly, or planted marsh samphire in order to desalinate the clay.
While the production of clay from sludge is by no means new, there has never been serious research into the process. Furthermore, it often took more than five years before the clay was suitable for use. An added factor is that the sludge comes from the silty Wadden Sea, whereas clay is generally produced from river sludge. Overly salty clay is unsuitable for dike reinforcement, and the salt therefore needs to be removed one way or another during the drying process.
'We aim to monitor this process carefully to see exactly what happens and to register the effect of differences between the various pits.' Drones will record the progress from the air, and the depot contains settlement rods and gauge pipes in order to monitor the development of the clay. The consortium hopes to have gained effective insight into the clay drying process in three years. 'By then, we'll know what works best, and can apply it elsewhere in the future.’
If you found this article interesting, subscribe for free to our weekly newsletter!