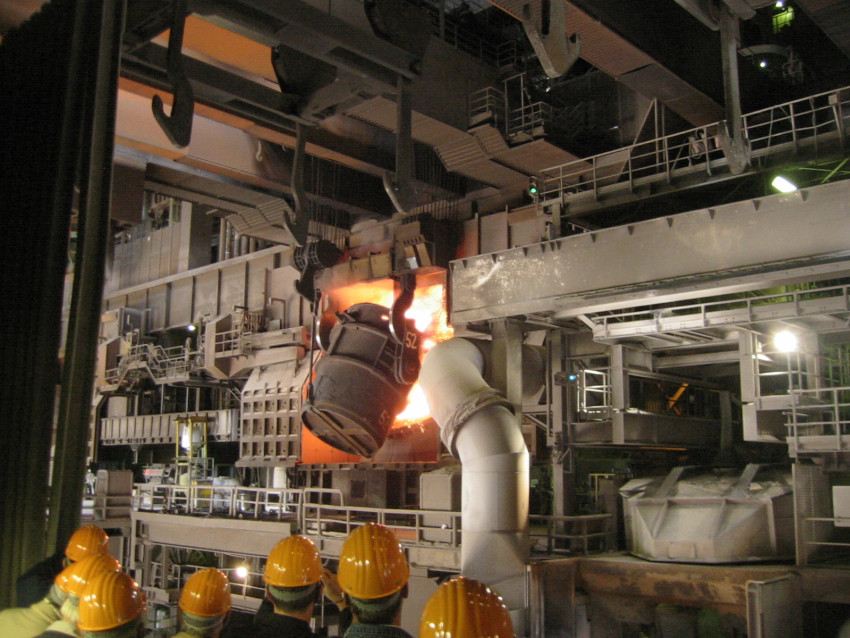
Duits CO2 industrie-initiatief
Negentien bedrijven en onderzoeksinstellingen uit de Duitse chemische en staalindustrie slaan de handen ineen om de CO2-uitstoot te verminderen. Ze gaan het bij staalproductie ontstane koolstofdioxide gebruiken in chemische processen.
De Duitse regering trekt zestig miljoen euro subsidie uit voor het project, en de samenwerkende bedrijven leggen daar komende tien jaar nog eens honderd miljoen bij. Einddoel van de samenwerking is een grootschalig staal- en chemiecomplex dat bij ThyssenKrupp in Duisburg moet komen.
Een derde minder CO2
In theorie vermindert dit systeem de uitstoot van de staalindustrie met een derde, wat neerkomt op ongeveer 20 miljoen ton CO2 per jaar minder. Die reductie is hard nodig, omdat zowel de chemische als de staalindustrie de grens bereikt op het gebied van uitstootreductie. Onderzoekers zoeken koortsachtig naar nieuwe ideeën om de nog steeds te hoge emissiewaarden omlaag te brengen. Carbon2Chem is zo’n idee. ‘Dit onderzoek is erop gericht om CO2 te besparen, bedrijven meer stabiliteit te geven en zo veel mogelijk economisch nut te halen uit duurzaamheid.'
Van koolstof naar chemie
Carbon2Chem laat zien dat fundamenteel onderzoek is om te zetten in nuttige toepassing wanneer verschillende instituties en branches met elkaar samenwerken. We laten nu zien dat een gesloten CO2-kringloop mogelijk is’, aldus prof.dr. Robert Schlögl, directeur van het Max-Planck-Institut für chemische Energiekonversion en een van de hoofdcoördinatoren van het project.
Carbon2Chem zoekt naar een koppeling tussen de processen in de staalindustrie en de chemiewereld. Hoofddoel: de restproducten van de ene industrie (staal) als grondstof inzetten voor de andere industrie (chemie). Zo ontstaan uit de gassen die bij staalproductie vrijkomen producten als ammoniak, methanol en polymeren. Die zijn verder te verwerken tot kunstmest, kunststoffen en brandstof.
Technikum
Om dat te bewerkstelligen komt op het hoogoventerrein van ThyssenKrupp in Duisburg het gemeenschappelijke Technikum, waar experimenten, simulaties en tests worden uitgevoerd. Deze zomer zijn twee containers met gasanalyse-apparatuur geïnstalleerd. Het is de eerste concrete stap in het lange termijn onderzoeks- en ontwikkelingsproject. Het project bestaat uit zes onderzoeksgroepen met een overkoepelende werkgroep die alles aan het eind moet samenvoegen tot een geheel.
Twee groepen houden zich bezig met noodzakelijke technologieën die voor het hele project essentieel zijn: de ene groep onderzoekt de analyse en reiniging van de hoogovengassen, de andere kijkt naar de productie van grote hoeveelheden waterstofgas.
De overige vier groepen dragen elk verantwoordelijkheid voor de duurzame productie van bepaalde soorten chemische basisproducten: methanol, poly-alcoholen, polymeren en OME (oxymethylether, een diesel- en benzinevervanger met minder roetdeeltjes). Alle groepen worden geleid door een bedrijf en werken samen met meerdere wetenschappelijke partners.
Overschot
Belangrijk aspect van het project is de stroomvoorziening: de initiatiefnemers willen alleen maar overschotstroom opgewekt via zonnepanelen en windturbines gebruiken. Bij zonne- en windenergie ontstaan door de dag heen nu eenmaal pieken, en door het overschot naar de fabrieken te leiden gebruik je die pieken nuttig. ‘De chemie-industrie functioneert dan als energieopslag, als accu’, zegt dr. Peter Achatz, CTO bij ThyssenKrupp en de grootste aanjager van het project. Deze vorm van energieverbruik levert een bijdrage om het elektriciteitsnet te stabiliseren. Het gebruik van overschot is trouwens alleen van toepassing op de chemiekant, want staalproducenten maken gebruik van een eigen elektriciteitscentrale en zijn dus niet aangesloten op het elektriciteitsnet.
Restgassen
De echte innovatie zit in het geschikt maken van de restgassen uit de staalproductie voor de chemische industrie. Dat vereist de ontwikkeling van nieuwe soorten spectrometers en katalysatoren. De spectrometers zijn nodig om te zien wat er allemaal in zo’n restgas zit. Dat is nu alleen globaal bekend: CO, CO2, NOx, CH4, H2 en verschillende zware metalen dampen dagelijks uit de grote schoorstenen van staalovens. De spectrometers zijn nodig om de pakweg vijfhonderd zogeheten sporenelementen te identificeren en hun invloed op de chemische vervolgprocessen te bepalen.
Daarnaast wil men een beeld krijgen van de schommelingen in de kwaliteit van de hoogovengassen. Is dat eenmaal bekend, dan kunnen de onderzoekers katalysatoren ontwikkelen die met continu wisselende concentraties om kunnen gaan. Voor de chemische industrie is het namelijk belangrijk dat de gebruikte gassen zo zuiver mogelijk zijn – iets wat niet is te garanderen met restgassen. Met betere technologie is dat probleem echter op te lossen.
Waterstof
Verder moeten de katalysatoren snel ‘aan’ en ‘uit’ kunnen. De uitdaging is om een chemische fabriek te bouwen die niet continu draait, maar alleen als er elektriciteit beschikbaar is. De technische oplossing moet bovendien ook kosteneffectief zijn. Daarmee heeft het consortium een flinke klus voor de boeg. Voor de productie van chemische basisstoffen uit CO2 is veel waterstof (H2) nodig. Hoogovengassen bevatten daar echter maar weinig van. Dus moet H2 op locatie worden gemaakt. ‘De cijfers laten zien dat dat een uitdaging is’, zegt Schlögl. ‘Voor een industrieel project zijn er 250 grote elektrolysetorens nodig.
Die hebben een volume van 250 zeecontainers en ze verlangen 12 TWh stroom per jaar. Dat is ongeveer evenveel als de Duitse spoorwegen of de stad Berlijn verbruiken.’ Dat maakt het lastig om de H2-productie en de chemische processen op overschotelektriciteit te laten lopen. Naar schatting van Schlögl zouden er minstens vierhonderd extra windturbines nodig zijn om voldoende H2 te maken. Uiteindelijk moet Carbon2Chem een modulair systeem worden, waarvan elk onderdeel apart is te verkopen. Dan kunnen ook andere grote CO2-producenten, zoals elektriciteitscentrales of papier- of cementfabrieken, profiteren van het onderzoekswerk van Carbon2Chem.
AkzoNobel doet ook mee
Ook Nederland is betrokken bij het project: AkzoNobel is een van de negentien deelnemers van Carbon2Chem. Het bedrijf heeft in Duitsland verschillende zoutelektrolysefabrieken staan die waterstof kunnen terugwinnen, en heeft hoge verwachtingen van het project. ‘Wij zijn altijd op zoek naar alternatieve, duurzame bronnen van stoffen als methanol en azijnzuur. Het voordeel van hoogovengassen is dat er zo veel van is. De gassen van de ThyssenKrupp-fabriek in Duisburg alleen al kunnen veel methanol per jaar opleveren’, vertelt Marco Waas, CTO bij het Nederlandse chemiebedrijf. AkzoNobel kan dankbaar gebruik maken van die gassen.
Daarnaast denkt het bedrijf ook zeker iets bij te kunnen dragen. ‘We hebben veel kennis opgebouwd over het produceren van grondstoffen uit de gassen die ook uit de hoogovens komen.’ AkzoNobel gaat de werkgroep rond methanolproductie coördineren. Dat betekent ook dat het bedrijf alle kleine uitvindingen op dat terrein moet samenvoegen tot een bruikbaar geheel. ‘Vooral integratie met de gasreinigingsdivisie is voor ons belangrijk. Voor methanolproductie heb je schoon gas nodig.’
Geen versnippering
Daar ligt ook meteen het grootste probleem van het project, zo voorziet Maas. ‘Dat de staalindustrie leidend is, vormt voor ons een uitdaging. De gaskwaliteit kan namelijk nogal schommelen, dus daar moeten we een oplossing voor vinden. Ook het produceren van waterstof zal lastig kostenefficiënt zijn te maken.’
Initiatieven zoals deze zijn niet nieuw. Wat wel nieuw is, is de enorme hoeveelheid steun die dit initiatief krijgt vanuit overheid en industrie. Niet eerder waren zo veel grote bedrijven betrokken bij een dergelijk project. Maas: ‘Bovendien zijn er veel middelen beschikbaar voor een duidelijk doel. Daar zouden wij in Nederland nog iets van kunnen leren. Wij hebben de neiging om de middelen te versnipperen.’ (Judith Stalpers)